Таблица 3.
Предельно допустимые из носы и зазоры в основных сопряжениях деталей двигателей мотоциклов «Днепр» и «Урал»Передняя цапфа коленчатого вала (сборного) изготовлена из стали ЗОХГСА и имеет твердость HRC 29-33. Если биение поверхности А относительно оси цапфы более 0,05 мм на радиусе 65 мм и имеется" износ той же поверхности при толщине щеки цапфы менее 17,86 мм, то цапфу заменяют (см. рис. 36),
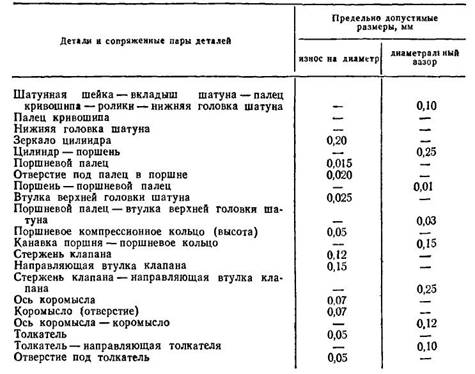
увеличение диаметра отверстия под палец более 35,86 мм — обработать поверхность отверстия до ближайшего ремонтного размера под ремонтный палец кривошипа;
износ поверхности цапфы под зубчатое колесо до диаметра менее 30 мм — устранить электронатиранием или хромированием;срыв резьбы отверстия более двух ниток — рассверлить отверстие и нарезать резьбу М16Х1.5 под ввертыш с нормальной резьбой М8Х1.
Задняя цапфа коленчатого вала изготовлена из стали ЗОХГСА, имеет твердость HRC 29-33. Если имеется биение поверхности В относительно оси более 0,05 мм на радиусе 65 мм или износ той же поверхности до толщины цапфы менее 17,86 мм, последняя подлежит замене. Задняя- цапфа может иметь следующие дефекты:износ боковых поверхностей шпоночного паза по ширине до 6 мм — подогнать шпонку по месту с обеспечением допустимой посадки, при износе паза до ширины более 6 мм заварить и обработать шпоночный паз до нормального размера 61о,о55 мм;
износ поверхности цапфы под подшипник до диаметра менее 34,98 мм — электронатирать или хромировать поверхность цапфы и довести до нормального размера;износ поверхности отверстия под палец до диаметра более 35,86 мм — обработать отверстие до ближайшего ремонтного размера под палец кривошипа, выдержав конусность 1; 140;
износ конусной поверхности цапфы под маховик более допустимого (допускается посадка конусного калибра на расстояние не менее 17,4 мм от опорной поверхности подшипника цапфы) — устранить электронатиранием или хромированием с последующей обработкой конусной поверхности до нормального размера (обработку желательно проводить при собранном узле).• Щека коленчатого вала изготовлена из стали ЗОХГСА и имеет твердость HRC 34-88. Если вследствие износа торцовых поверхностей толщина щеки менее 17,86 мм, ее заменяют. При ремонте щека может иметь следующие дефекты:
износ поверхностей отверстий под палец более 35, 88 и 40 мм (соответственно для мотоциклов «Урал-3»М-66 и«Урал»М-67-36)—• непараллельность осей отверстий более 0,05 мм на длине 100 мм;неперпендикулярность осей отверстий относительно торцовых поверхностей щеки более 0,04 мм на длине 100 мм — обработать поверхности отверстий до ближайшего ремонтного размера под ремонтный палец, при растачивании отверстий щеки ее отбалансировать. Неуравновешенность относительно оси должна быть не более 8-Ю-4 Н-м.
Передний корпус подшипника изготовлен из стали 20. Если на корпусе имеются трещины, его заменяют. При ремонте может иметь следующие дефекты:износ поверхности отверстия под подшипник до диаметра более 72,02 мм — устранить электронатиранием или хромированием и обработать до нормального размера;
износ поверхности корпуса подшипника под картер до диаметра менее 77,01 мм — поверхность корпуса хромировать или обварить и затем обработать до нормального или ремонтного размера:Цельный коленчатый вал (рис. 35) изготовлен из высокопрочного чугуна ВЧ 50-2 и имеет прочность НВ 215-255. Если вал имеет трещины, его заменяют. При ремонте вал может иметь следующие дефекты:
износ, овальность и конусность шатунных шеек;износ конусов поверхности под маховик более допустимого (допускается посадка калибра на расстояние не менее 17,4 мм от опорной поверхности подшипника вала);
срыв резьбы более двух ниток под болт крепления маховика;износ поверхности вала под ролико- и шарикоподшипники до диаметра менее 49,94 мм;
износ поверхности вала под корпус подшипника до диаметра менее 33,95 мм;износ поверхности под ведущее зубчатое колесо распределения и корпус центрифуги до диаметра менее 26,98 мм;
износ шпоночных пазов по ширине более 3,985 мм (под зубчатое колесо распределения) и 5,985 мм (под маховик);срыв резьбы более двух ниток под болт крепления центрифуги.
В ремонтной практике существует несколько способов ремонта и восстановления шеек коленчатых валов: перешлифовка их под ремонтные размеры, хромирование до нормального или ремонтного размера, осталивание с последующим хромированием, автоматическая электровибрационная наплавка в струе жидкости, механизированная наплавка под слоем флюса, автоматическая наплавка в струе углекислого газа и в струе воздуха, плазменная наплавка. Наиболее экономична перешлифовка шеек под ремонтные размеры, но при этом уменьшается их твердость.При подготовке коленчатого вала к перешлифовке его устанавливают в патрон токарно-винторезного станка типа 1А62 и поверхностью под подшипник — в люнет, выверяют биение, которое допуска^ ется не более 0,04 мм. Зачищают центровую фаску 2x30° на переднем конце вала резцом для растачивания центровых отверстий. После этого поворачивают вал на 180° и закрепляют в патроне и в люнете. Выверяют биение индикатором, проверяют и зачищают резцом центровую фаску 2X30°. Устанавливают вал на станок для шлифования, применяя приспособление смещения центров, и шлифуют шатунные шейки до одного из ремонтных размеров, указанных в таблице 9, выдержав размер галтелей 1,5...2 мм и размер по длине
28.5+0-14 мм. Полировать шатунные шейки коленчатых валов следует, применяя специальные хомуты и пасты; особенно рекомендуются алмазные ленты АСО10 на связке Р9. Режим обработки: частота вращения вала—100...200 мин-1, давление — 300...600 кПа, охлаждение— керосином, шероховатость поверхности шеек — не более 0,16 мкм, овальность и конусность шеек — не более 0,004 мм.Износ посадочных мест под ролико- и шарикоподшипники восстанавливают хромированием, затем шлифуют поверхность до нормального размера 45±0-008 мм; износ конусной поверхности также восстанавливают хромированием и шлифуют конусность 1:5с проверкой на краску; прилегание должно быть не менее 60% поверхности конуса. При срыве резьбы отверстие рассверливают, заваривают, вновь просверливают и нарезают резьбу нормального размера. Износ поверхности под корпус подшипника, под зубчатое колесо распределения и корпус центрифуги восстанавливают хромированием дефектной поверхности и шлифуют ее до нормального размера. Шпоночные размеры восстанавливают так же, как пазы в передней и задней цапфах кривошипа.
Сильно изношенный коленчатый вал можно восстановить хромированием или плазменной наплавкой. Перед наплавкой смазочные линии замазывают смесью шамотной глины и асбеста или пастой, состоящей из 85% графита и 15% жидкого стекла. Наплавляют сначала по шатунным, а затем по коренным шейкам. За базу берут посадочные места под подшипники. Твердость наплавленного металла должна быть HRC 52-56. Для этого можно использовать электродную проволоку 15ГСТЭЦА диаметром 1,5... 1,6 мм. Перед употреблением проволоку обезжиривают. Режим наплавки шеек: сила тока — 150... 180 А, напряжение — 27...30 В, частота вращения шпинделя станка — 2Д..3.0 мин-1, шаг наплавки — 2.5...3 мм/об, индуктивность— 16 витков дросселя РСТЭ-34, вылет электрода—15...18 мм, смещение электрода с зенита — 20...25 мм.После наплавки коленчатый вал обдирают шлифовальным кругом КЧ-К46-СМ2. Окружная скорость шлифовального круга — 25...30 м/с, вала—12...15 м/мин. Окончательно шлифуют под номинальный размер на тех же режимах, но подачу уменьшают до 0,01 мм/об. Затем вскрывают смазочные линии твердосплавным сверлом диаметром 12... 13 мм, калибруют резьбу и исправляют шпоночные пазы. После этого снимают фаски с острых кромок смазочных линий шатунных шеек, промывают теплой водой и продувают сжатым воздухом, удалив абразивный порошок и металлическую пыль.
Биение торцов Ti и Тг на радиусе 29 мм относительно оси коленчатого вала допускается до 0,04 мм, биение торца Т на радиусе 16 мм относительно оси — не более 0,04 мм. Относительная непараллельность осей шатунных и коренных шеек не должна превышать 0,05 мм на длине 100 мм, смещение шпоночных пазов с диаметральной плоскости и плоскости осей шатунных шеек — 0,01 мм. После ремонта коленчатый вал подвергают динамической балансировке с точностью 1•10~3 Н • м.Шатуны изготовлены из стали 12ХНЗА и имеют твердость нижней головки HRC 58-62, а верхней и стержня — НВ 80-98. При ремонте устраняют следующие дефекты:
износ поверхности отверстия под втулку до диаметра более 23,53 мм — поверхность отверстия обработать до ремонтного размера 23,6+0>023 мм под ремонтную втулку;износ поверхности отверстия под ролики до диаметра более 50,03 мм—поверхность отверстия обработать до ближайшего ремонтного размера 50.2+0.012; 50.4-W12; 50,6+°.°12; 50,8+°.°12; 51,QW12 мм под нормальные ролики с ремонтным пальцем кривошипа; при конусности или эллипсности отверстия нижней головки шатуна более допустимого (допускается конусность или эллипсность не более 0,005) отверстие обработать до ближайшего ремонтного размера. Если износ поверхности отверстия нижней головки шатуна требует обработки иод ролики третьего ремонтного размера, эту поверхность необходимо цементировать на глубину 0,7..Л мм и затем шлифовать под ремонтный размер. Остальные поверхности шатуна от цементации предохраняют;
непараллельность осей верхней и нижней головок шатуна более 0,16 мм на длине 100 мм — выправить шатун до устранения дефекта;непрямолинейность стержня шатуна более 0,3 мм на длине 70 мм — выправить шатун до устранения дефекта;
износ отверстия под болт до диаметра более 8,26 мм — развернуть отверстие до ремонтного размера 8,33; 8,43; 8,53; 8,63, 8,73 мм под ремонтный болт;износ торцовой поверхности нижней головки шатуна по ширине до размера менее 28,25 мм — хромировать или электронатирать поверхность и затем шлифовать до нормальной ширины 28,205... 28,350 мм.
Если износ втулки верхней головки шатуна превышает допустимую величину, выпрессовывают изношенную втулку оправкой под ручным прессом. Втулки верхней головки шатуна поставляют только одного размера, свернутыми из бронзовой ленты ОПС4-4-2,5 толщиной 1 мм. При износе отверстия шатуна под втулку до диаметра более 23,53 мм его можно восстановить электронатиранием под втулку нормального размера.Шатуны с разъемной нижней головкой при износе отверстия до диаметра более 51,53 мм можно восстановить нанесением эпоксидной пасты с последующим растачиванием до нормального размера. Запрещается опиливать или шабрить стыки, так как нарушается геометрическая форма подшипников, ухудшается теплоотвод от них, и вкладыши быстро изнашиваются. Кроме того, в нижнюю головку шатуна со спиленными или шабренными стыками в дальнейшем нельзя установить вкладыши ремонтных размеров. Испорченные этими операциями крышки подшипников не могут быть заменены новыми, поскольку последние обработаны на заводе совместно с шатуном.
Оси отверстий верхней и нижней головок шатуна должны лежать в одной плоскости с точностью до 0,05 мм на длине 100 мм. Непараллельность осей в этой плоскости допускается не более 0,03 мм на длине 100 мм.По диаметру отверстия верхней головки шатуны (с втулкой) принято сортировать на четыре группы (табл. 4). Цветовой индекс группы наносят краской на внутренней поверхности стержня шатуна возле верхней головки.
Таблица 4.Цветовые индексы групп и диаметры отверстий верхней головки шатуна (с втулкой), мм
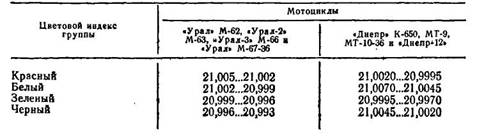
Шатуны по диаметру отверстия нижней головки в пределах каждого размера принято сортировать по группам и маркировать краской (табл. 5). Цветовой индекс наносят на внутренней поверхности стержня шатуна у нижней головки. При эллипсности и конусности отверстия в головках шатуна в допустимых пределах относят к той или иной группе по наименьшим размерам. Измеряют при температуре окружающей среды 15...25СС.
У шатунов с отверстием нижней головки ремонтного размера удаляют старую и наносят травлением новую цифру, соответствующую массе нижней головки с точностью до 1 г. Цифру вытравляют на наружной поверхности головки (со стороны канавки на торце). Например, если масса нижней головки (определяют на специальных спаренных весах, на которых шатун укладывают каждой головкой на отдельную чашу весов) равна 200,1 г, то наносят цифру 200, приТаблица 5.
Цветовые индексы групп и диаметры отверстий нижней головки шатуна, ммТаблица б.
Цветовые индексы групп и диаметры пальцакривошипа, мм
Кривошипный механизм. При сборке кривошипных механизмов двигателей мотоциклов серии «Урал» и «Днепр-12» необходимо подобрать по массе два шатуна, имеющих одинаковые клейма на нижней головке. Массу нижней головки шатунов для двигателей мотоциклов «Урал» М-62 и «Урал-2» М-63 в граммах обозначают на ее наружной поверхности цифрами 200, 202, 204, 206, 208, а для мотоциклов «Урал-3» М-66 и «Урал» М-67-36 — цифрами 224, 226, 228, 230 и 232. Затем подбирают с соответствующими цветовыми индексами пальцы кривошипов, запрессовывают их в переднюю и заднюю цапфы с натягом 0,124...0,170 мм. Расположен ние отверстий «а» для смазки диаметром 2,5...3 мм в пальцах должно соответствовать указанному на рисунке 36.
Комплект роликов для шатунов двигателей мотоциклов «Урал» М-62, «Урал-2» М-63 и «Днепр-12» подбирают в соответствии с цветовыми индексами (размерными группами) пальца кривошипа и отверстия нижней головки шатуна (табл. 7).
При установке шатунов, имеющих допустимый износ поверхности под ролики, их комплектуют с пальцами кривошипа, обозначенными красным индексом, и подбирают группу роликов, обеспечивающих зазор в подшипнике 0,010...0,025 мм.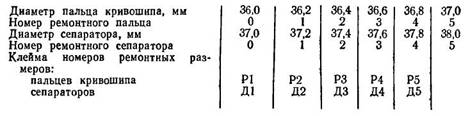
Таблица 8.
Группы роликов шатунаСпециальное приспособление должно обеспечивать соосность шеек Л и Б (см. рис. 36) и расположение пальцев в плоскости, проходящей через оси этих шеек. Технологический процесс охлаждения кривошипного механизма должен исключать снижение твердости рабочей поверхности пальца кривошипа. Биение поверхностей А и В при установке механизма в центрах допустимо не более 0,03 мм. Измеряют его на расстоянии 5 мм от шейки. При биении более 0,03 мм допускается правка. После сборки коленчатого вала шлифуют коренные шейки цапф и конус под маховик до нормальных размеров, под подшипник — диаметром 35_0,oi7 мм и под зубчатое колесо распределения— до диаметра 30+одш мм. Затем устанавливают маслоуловитель, затягивают крепящие винты до упора и раскернивают в шлиц с одной стороны металлом маслоуловителя.
Если биение коренных шеек превышает указанную величину, то коленчатый вал необходимо править с контролем на приспособлении с центрами и индикаторами (рис. 37). Стрелки обоих индикаторов" должны отклоняться в одном направлении в ту или другую сто-рону от нуля (см. рис. 37,б,в). Если стрелки показывают разные величины (см. рис. 37,а), то определяют наиболее высокую точку на коренной шейке (см. на рис. 37, а — левая шейка) и, зажав ще« ку коленчатого вала в тиски, не сильно ударяют свинцовым или медным молотком по левой цапфе (стрелку см. на рис. 37). Если стрелки индикаторов показывают одинаковое минусовое отклонение, превышающее допустимую величину, то удары молотком наносят вовнутрь (стрелки см. на рис. 37,6). При плюсовом отклонении
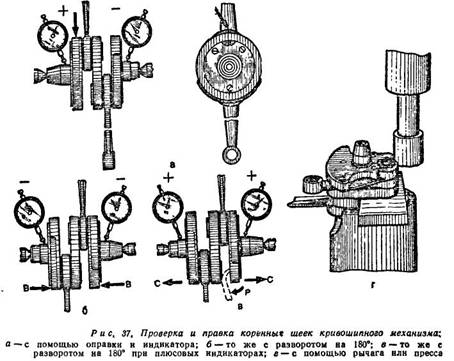
Разворот коленчатого вала проверяют в центрах индикатором. Для этого в верхние головки шатунов вставляют оправку (рис.38), соответствующую цветовому индексу отверстий головок. Замеряют в двух положениях коленчатого вала (см. рис. 38, а,б). Разница в замерах не должна превышать 0,5 мм. В случае большей величины коленчатый вал правят ударами молотка по соответствующим сторонам цапф. Правка шатунов собранного коленчатого вала недопустима. При проверке коленчатого вала «по методу треугольника» разность показаний индикатора не должна превышать 0,5 мм. Радиальный зазор нижней головки шатуна должен быть не более 0,012 мм, осевой зазор нижней головки шатуна на пальце кривошипа — 0,05... 0,034 мм. Шатуны должны проворачиваться свободно, без заеданий.
Для сборки коленчатых валов мотоциклов серии «Днепр» подбирают шатуны в сборе по массе с одинаковым цветовым индексом из пяти групп: синий — 530±2,5 г, зеленый —535±2,5 г, красный — 540±2,5 г, черный — 545±2,5 г, белый — 550±2,5 г. Цветовой индекс наносят на наружной поверхности крышки шатуна.Коленчатый вал МТ801201 должен быть нормального или ремонтного размера в комплекте с нормальными или ремонтными вкладышами. Перед сборкой вала смазочные линии продувают сжатым воздухом. Собранный коленчатый вал с пробками МТ801-201 и винтом 242503П8 раскернивают в двух местах и балансируют динамически
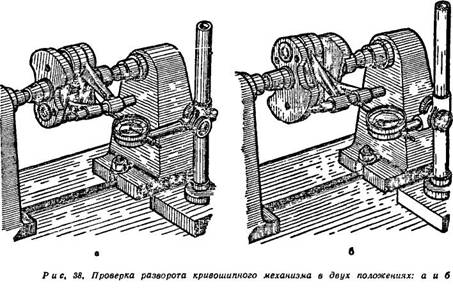
Шатуны на коленчатый вал устанавливают выступами на стержнях шатунов (указаны стрелками на рис. 39), направленными у первого шатуна вперед и у второго — к маховику. Поверхность вкладышей считается удовлетворительной, если на ней нет задиров, выкрашиваний и вдавленных инородных материалов. Темная окраска поверхности не является браковочным признаком.
Вкладыши, пригодные для дальнейшей эксплуатации, должны быть упругими, чтобы размещаться в постели крышек шатунных подшипников с натягом, необходимым для теплоотвода от вкладышей к поверхности постели. Вкладыши, не имеющие натяга в постелях, заменяют. Для замены изношенных или поврежденных вкладышейотполированы до ближайшего ремонтного размера (табл. 9). Если применение вкладышей ремонтных размеров не обеспечит получение необходимых зазоров в подшипниках шатунов (в случаях, когда вал уже прошлифован до максимального уменьшения диаметра шеек), устанавливают новый коленчатый вал с вкладышами нормального размера.
Таблица 9.Размеры шатунной шейки коленчатого вала и соответствующего вкладыша
Вкладыши при ремонте двигателя заменяют на новые без каких-либо подгоночных операций и только попарно. Замена одного вкладыша не допускается.Цилиндр двигателя мотоциклов К-750М и «Днепр-12» изготовлен из специального чугуна твердостью НВ 207-255. Если цилиндр имеет обломы ребер общей площадью более 15%, сколы кромок выпускных и впускных патрубков по внутренней поверхности глубиной более 10 мм, износ конусной поверхности седла клапана при утопании конусного калибра относительно торца более 2 мм, то такой цилиндр заменяют. Допускается наварить и обработать дефектные места до нормального размера. Кроме того, у цилиндра при ремонте могут быть следующие дефекты:
риски, задиры, раковины на конусной поверхности седла клапана— обработать поверхность седла до устранения дефекта, но до размера, при котором утопание конусного калибра относительно торца седла клапана будет не более 2 мм;коробление плоскости разъема с головкой цилиндра более 0,1 мм — обработать плоскость до устранения дефекта, но до размера не менее 134,06 мм, а у мотоциклов «Днепр»—102 мм и «Урал»—94 мм;
износ поверхности зеркала цилиндра — замерить внутренний диаметр цилиндра нутромером в пяти поясах на расстояниях 9. 16, 64, 74, 84 мм от верхней плоскости цилиндра в двух плоскостях: в плоскости качания шатуна и в плоскости, перпендикулярной ей; если овальность зеркала цилиндра превышает 0,07 мм, а конусообраз-ность или износ превышает 0,15 мм, то цилиндр нуждается в расшли-фовке под ближайший ремонтный размер поршня. Окончательно доводят поверхность зеркала цилиндра хонинг-процессом. Овальность и конусообразность допускается не более 0,015 мм, неперпендикулярность оси зеркала цилиндра к опорной плоскости фланца цилиндра не должна превышать 0,06 мм на длине 100 мм;забоины на плоскости разъемов с картером — зачистить дефектную плоскость до устранения дефекта, но до размера «а» не менее 134,06 мм, а для мотоциклов «Днепр»— 102 мм и «Урал»—94 мм;
ослабление посадки шпилек при срыве резьбы в отверстии более двух ниток — рассверлить отверстие и нарезать резьбу ремонтного размера М10 под ремонтную шпильку.Для растачивания цилиндр устанавливают в патрон токарного станка типа 1А62 и растачивают резцом с пластиной из твердого сплава ВК-2 со скоростью резания 137 м/мин, при частоте вращения шпинделя 475 мин-1 и подаче 0,125 мм/об. Припуск на хонингование должен быть 0,04...0,06 мм. Зеркало цилиндра можно хонинговать на вертикально-хонинговальном станке ЗА833 с применением абразивных брусков К3120СТ2-Т2К, К3180СТ2К при предварительной обработке и К3280СМ2-С1Б, К3400СМ2 и М20СТ2-Т2К — при окончательной обработке.
Режим работы на станке: частота вращения шпинделя — 180 мин-1, скорость резания — 51 м/мин, скорость возвратно-поступательного движения хонинговальной головки — 20 м/мин.При хонинговании обильно подают охлаждающую жидкость — керосин или смесь керосина с 10...20% машинного масла. Оба цилиндра обрабатывают только под один ремонтный размер. При отсутствии хонинговального станка эту обработку можно проводить на токарном или радиально-сверлильном станке, применяя при этом хонинговальную головку с пружинами под брусками.
После окончания обработки зеркала цилиндра для удаления с него абразивной пыли поверхность его промывают теплой мыльной водой и волосяной щеткой или керосином и щеткой, затем сушат на воздухе. Шероховатость поверхности зеркала цилиндра должна быть не более 0,32 мкм; чтобы повысить износостойкость и уменьшить шероховатость поверхности зеркала цилиндра, его можно обкатать виброшариком. На рисунке 40 показаны отремонтированные цилиндры двигателей мотоциклов «Днепр» К-650, МТ-9, МТ-10-36 и серии «Урал» с запрессованными гильзами, а на рисунке 41 — цилиндры мотоциклов К-750М и «Днепр-12».Поршневые кольца. Перед установкой новых поршневых колец их необходимо подогнать по канавке поршня (см. с. 61). Зазор в замке замеряют у кольца, вставленного в цилиндр без перекосов. Положение кольца в цилиндре удобно выравнивать поршнем, вводимым вслед за кольцом. Зазор должен быть для компрессионных колец 0,04...0,08 мм (только для новых), для маслосъемных — 0,025..Д065 мм. При установке поршневых колец в цилиндр не должно быть светового зазора по окружности между кольцом и цилиндром, допускается просвет до 0,12 мм на общей длине не более V* окружности.
В случае отсутствия поршневых колец заводского изготовления их можно изготовить из литой толстостенной трубы мелкозернистогочугуна с наружным диаметром 80...85 мм и диаметром отверстия 55...60 мм. Трубу закрепляют в патроне токарного станка и за один установ протачивают по наружному и внутреннему диаметру, обес-печивая шероховатость поверхности 0,63 мкм. Затем отрезают кольца с небольшим припуском на доводку. Подогнанное кольцо разре-
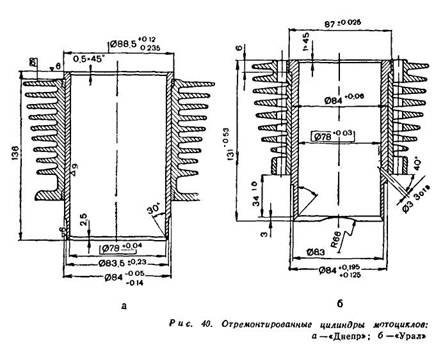
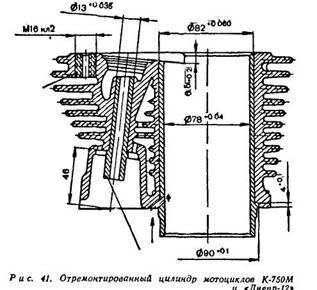
При сборке кольца надевают на поршень последовательно, с помощью специального приспособления или пластин, обеспечивающих минимальный развод колец в стыках. Надетые кольца должны свободно перемещаться в канавках поршня. Это проверяют встряхиванием поршня, промытого керосином; кольца должны свободно западать в канавки поршня.
Поршень. Допустимый износ отверстия под поршневой палец не должен превышать 0,02 мм. При наличии износа отверстия под поршневой палец и канавок под поршневые кольца более допустимых, а также при наличии задиров на юбке поршни заменяют. При первой замене поршней в незначительно изношенных цилиндрах, не требующих расточки и шлифовки, устанавливают поршни нормального размера группы, соответствующей фактическому размеру цилиндра. При расточке цилиндров устанавливают поршни соответствующего ремонтного размера, обеспечивая зазор между юбкой поршня и зеркалом цилиндра 0,08...0,10 мм. Наряду с подбором поршня к цилиндру по диаметру юбки следует подбирать их по весу. Это необходимо для уравновешенности двигателя. Разница в весе поршней двигателя не должна превышать 4 г. Взвешивать надо поршень в сборе с кольцами и пальцем. У подобранных поршней цветовая маркировка отверстий под поршневой палец должна соответствовать маркировке отверстия верхней головки шатуна. Маркировочную краску наносят на поршнях на нижнюю поверхность одной из бобышек, на шатунах — у верхней головки. Это позволит правильно подобрать поршневой палец.Поршневой палец. Осматривают наружную поверхность пальца, проверяют, нет ли рисок, забоин, наволакивания бронзы и ощутимого износа. Износ поршневого пальца замеряют по краям и в середине, износ не должен превышать 0,015 минимального размера цветовой маркировки. При замене коленчатого вала, втулки в верхней головке шатуна, поршня или самого пальца новый палец подбирают по цветовой маркировке (нанесена на внутреннюю поверхность с одного конца), которая должна соответствовать цветовой маркировке отверстий поршня и верхней головкн шатуна.
Поршневой палец можно восстановить хромированием с последующим шлифованием до нормального размера 21Io!oi4 или допустимого 20,986 мм с обеспечением при сборке зазора во втулке верхней головки шатуна 0,0045...0,0095 мм и натяга в бобышках поршня 0,0045...0,0095 мм.Головка цилиндра. Осматривают все доступные места в головке цилиндра, проверяют, нет ли поломок, трещин, прогаров,
срывов ниток резьбы, плоскостность поверхностей крепления головки к цилиндру, карбюратору. Головка цилиндра двигателей мотоциклов К-750М и «Днепр-12» изготовлена из алюминиевого сплава АЛ10В твердостью НВ 65. Если головка имеет трещины, обломы любого размера и расположения (кроме трещин и обломов ребер), срыв резьбы более двух ниток в футорке под свечу зажигания, то ее заменяют. При ремонте головка может иметь следующие дефекты:трещины, обломы ребер общей площадью до 15% оребрения — зачистить места обломов;
коробление плоскости разъема головки с цилиндром более 0,075 мм — обработать плоскость до устранения недопустимого коробления.Для осмотра головки цилиндра у двигателей мотоциклов «Урал» и «Днепр» (рис. 42) снимают с помощью съемников (см. рис. 26) клапаны. Если они отсутствуют, поступают следующим образом: устанавливают головку с клапанами на деревянную опору; прикладывают к подпятнику пружины отрезок металлической трубки с внутренним диаметром, достаточным для свободного прохода сухариков, и слегка ударяют молотком по концу трубки; оба сухарика выйдут из своего гнезда после одного-двух ударов. Затем снимают верхние тарелки пружин, пружины и нижние тарелки и вынимают клапаны. Головка может иметь дефекты:
износ отверстия в направляющей втулке до диаметра более 8,13 мм — развернуть отверстие под ремонтный стержень клапана;ослабление посадки направляющей втулки — обработать отверстие до ближайшего ремонтного размера 14,1+°>035; 14,2+°-035; 14,3+°-°35; 14,4+°-035; 14,5+°>035 мм под ремонтную втулку;
ослабление посадки седла выпускного клапана при износе посадочного отверстия в головке до диаметра более 38,07 мм — обработать отверстие до ближайшего ремонтного размера;износ поверхности отверстия под ось коромысла — обработать отверстие под ремонтный размер 10,105; 10,205; 10,305; 10,405; 10,505 мм под ремонтную ось коромысла;
ослабление посадки штифтов — заменить дефектный штифт. Допускается посадка штифтов на железном сурике;ослабление посадки оси коромысла при износе посадочного отверстия в головке до диаметра более 15,045 мм — заменить стойку или развернуть отверстие до ремонтного размера 15,1-ьо.°з5 мм под ре_ монтную стойку;
ослабление посадки патрубка — заменить патрубок, обеспечив натяг 0,04 мм;срыв резьбы на шпильках более двух ниток — заменить шпильку.
Для замены направляющей втулки головку цилиндра закрепляют в тисках, вставляют оправку и выпрессовывают направляющую втулку, клапана; проверяют состояние отверстия под направляющую втулку; нагревают головку до 200°С и, надев направляющую втулку на оправку, запрессовывают втулку на место, выдержав 20 мм от плоскости опоры нижней тарелки пружин до кромки втулки; развертывают отверстие направляющей втулки разверткой до 8,00...8,03 мм и проверяют прямолинейность отверстия калибром диаметром 7,98 идлиной 50 мм. Калибр должен проходить под собственной массой по всей длине втулки. Если втулки металлокерамические, их перед запрессовкой необходимо пропитать в масле двигателя в течение 1.5...2 ч.
После ремонта направляющей втулки в обязательном порядке проверяют несоосность фаски седла клапана и при необходимостиКлапаны изготовлены из стали 4Х9С2, 4Х9Г2, 5Х20Н4АГЭМ и имеют твердость поверхности стержня HRC 48-54, остальной части НВ 255-302. При наличии трещин и обломов клапан заменяют.
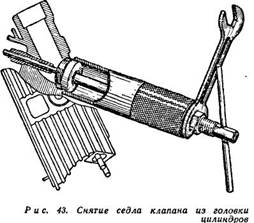
прогорание, задиры, забоины или износ поверхности конуса тарелки при высоте цилиндрической части более 0,5 мм — проточить поверхность тарелки, но до размера цилиндрического пояска не менее 0,5 мм и диаметра тарелки не менее 37,2 мм;
износ поверхности стержня клапана до диаметра менее 7,85 мм —восстановить поверхность стержня хромированием и шлифовать до размера, обеспечивающего нормальный либо допустимый зазор 0,2 мм с сопряженной деталью;
погнутость стержня клапана более 0,02 мм — выправить стержень на алюминиевой плите ударами свинцового молотка до устранения недопустимой погнутости;местный износ, забоины на торцовой поверхности стержня клапана — обработать поверхность до устранения дефекта, но до размера по длине не менее 136,3 мм для мотоциклов К-750М и «Днепр-12», не менее 90,7 мм у выпускного и 91,7 мм у впускного — для мотоциклов «Урал» и не менее 91,8 мм — для мотоциклов «Днепр».
Если седла и головки клапанов незначительно изношены и клапан прилегает по всей поверхности, а поясок прилегания находится в пределах 1,5...1,8 мм, можно ограничиться чисткой и притиркой рабочих фасок клапана и седла.Если седло клапана имеет большую выработку или другие изъяны и шлифовкой не удается вывести их, то седло клапана заменяют новым, для чего необходимо: специальным метчиком нарезать резьбу в седле клапана, затем нагреть головку до 200°С, завернуть винт съемника, как указано на рисунке 43, и вынуть седло. Можно разрезать седло на три части наждачным диском и вынуть его по частям, затем расточить гнездо под один из ремонтных размеров с помощью приспособления (рис. 44) или подогнать ремонтное седло к старому отверстию с учетом допустимого натяга 0,2...0,25 мм. Ремонтные размеры гнезда седла —38,3+0-05; 38,4+°.°5; 38,5+°.°5; 38,6+°.°5; 38,7+°05 мм (только для мотоциклов «Урал»), Для впускного клапана мотоциклов «Урал» и обоих клапанов мотоциклов «Днепр» обрабатывают посадочное отверстие до ремонтных размеров 41,3+0>05;
41,4+0,03. 41,5+0,05; 41,6+005; 41,7+о.<и мм такЖе под ремонтное седло клапана.Перед запрессовкой седло охлаждают в жидком азоте до температуры минус 75...100°С и с помощью оправки запрессовывают в гнездо до упора. Чугунное седло перед запрессовкой смазывают насыщенным раствором нашатыря, а бронзовое — маслом для двига-
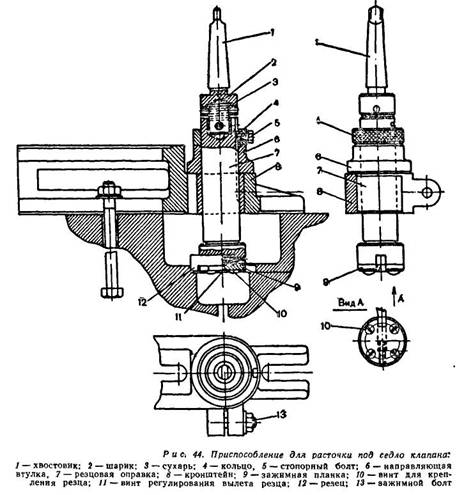
После притирки тщательно промывают клапаны, седла клапанов, направляющие втулки, горловину и камеру сгорания головок ци-
линдра до полного удаления притирочной пасты и протирают насухо. После этого проверяют герметичность посадки клапанов, для чего ставят клапаны на место и, прижимая головки клапана к седлу, поочередно заливают керосин во всасывающие и выпускные каналы головки цилиндра. Просачивания керосина не должно быть в течение 1 мин. При просачивании керосина ранее указанного срока требуется дополнительная, более тщательная притирка.Коромысла клапанов с осью. При снятии коромысел с осями и кронштейнами с головки цилиндра необходимо пометить их для постановки при сборке на старое место. Для разборки коромысел выпрессовывают ось коромысел из кронштейнов. После разборки коромысел клапанов детали промывают и подвергают осмотру и необходимым замерам. Проверяют, нет ли трещин, забоин, задиров на оси и в отверстии коромысла и других дефектов, износ осей коромысел и внутренних отверстий самих коромысел. При износе как осей, так и отверстий в коромыслах более 0,07 мм детали заменяют.
При наличии бронзовых втулок, запрессованных в отверстие коромысла, и увеличенном износе втулки заменяют новыми и после запрессовки развертывают до размера 15... 15,027 мм.Штанги. Вынутые штанги осматривают, проверяют, нет ли из-носов концов, каких-либо потертостей или других повреждений и непрямолинейности. При износе концов штангу заменяют. Незначительную непрямолинейность штанги, как исключение, разрешается править на поверочной плите легкими ударами молотка по стержню через оправку из мягкого металла. При проверке на поверочной плите щуп 0,2 мм не должен проходить между штангой и плитой. Общая длина штанги должна быть 233±1 мм.
Толкатели. Вынутые при разборке двигателя толкатели и направляющие толкателей промывают и тщательно осматривают. Толкатели изготовлены из специального чугуна и имеют твердость рабочего торца HRC 50-60, а остальной части — НВ 207-255. При износе поверхности под .направляющую до диаметра менее 13,95 мм, срыве резьбы более двух ниток и износе опорной поверхности по длине менее 68,5 мм для мотоциклов К-750М и «Днепр-12», менее 52,9 мм — для мотоциклов «Днепр» и менее 68,35 мм — для мотоциклов «Урал» толкатели заменяют. Зазор в сопряжении толкатель— направляющая толкателя не должен превышать 0,10 мм. При увеличенном зазоре толкатель или направляющую толкателя заменяют в зависимости от степени износа той или другой детали.Зубчатое колесо распределительного вала изготовлено из серого чугуна и имеет твердость НВ 170-229. Браковочным признаком служит износ зубьев до толщины менее 3,8 мм, а также износ поверхности отверстия под распределительный вал до диаметра более 22,025 мм. Допускается ремонт электронатиранием или хромированием поверхности отверстия с последующей обработкой до нормаль* ного размера 22+0-02S мм.
При ремонте зубчатое колесо может иметь следующие дефекты:износ шпоночного паза до ширины более 3,065 мм — обработать
паз до ремонтного размера 3,2да9; 3,4+ода; 3,6+о;<ш мм под ре-монтную шпонку. При износе паза до ширины 3,065 мм подогнать шпонку по месту с обеспечением посадки 0,08 мм (зазор);
разработка отверстия под штифт — развернуть отверстие до ремонтного размера 5,25Io;o55, 5,5Io;o5s; 5,751о;о55 5 6Го.ок мм под ремонтный штифт.Распределительный вал. Для замеров необходимы микрометры от 0 до 25 мм и от 25 до 50 мм. Распределительный вал изготовлен из стали 15, 20Х или 45 и имеет твердость кулачков HRC 43-48. Если зубчатое колесо изношено до толщины зуба 2,1 мм, поверхность кулачка до 15,88 мм по меньшей оси и до величины 36,46 мм по большей оси, то вал заменяют. Допускается износ кулачков распределения и зажигания. Устраняют его наплавкой сор-майта № 1 или № 2 в водяной ванне и обрабатывают до нормального размера с сохранением заданной твердости.
При ремонте распределительный вал может иметь следующие дефекты:риски, задиры, забоины на поверхности кулачка газораспределения— зачистить поверхность кулачка до устранения дефекта, но до размера не менее 36,46 мм;
износ поверхностей вала соответственно под зубчатое колесо до диаметра менее 22,035 мм, под сальник — до диаметра менее 15,8 мм, под втулки — до диаметра менее 15,8 мм и менее 21,93 мм, под подшипник— до диаметра менее 24,98 мм — хромировать и шлифовать поверхности до нормального размера;износ боковых поверхностей паза под ротор по ширине более 3,75 мм — заварить паз и фрезеровать до нормального размера;
износ боковых поверхностей шпоночного паза по ширине более 2,99 мм — подогнать шпонку по месту с обеспечением нормальной или допустимой посадки 0,006 мм (зазор).Кулачки распределительных валов восстанавливают в специализированных ремонтных предприятиях, где имеется специальный копировально-шлифовальный станок или кругло-шлифовальный станок с копировальным приспособлением.
При отсутствии указанных приспособлений кулачки распределительных валов восстанавливают следующим образом: изготовляют деревянный круг на токарном станке диаметром 180...200 мм и толщиной 25...30 мм, затем от наждачного полотна отрывают полоску шириной по толщине круга, а по длине такую, чтобы иметь возможность 2...3 раза его обмотать. В том месте, где полоска закончится, ее закрепляют двумя-тремя медными гвоздиками. Круг устанавливают на ось заточного станка или в центрах токарного станка. Станок запускают и аккуратно шлифуют по радиусу кулачки, только в местах их выработки.Смазочный насос. Зубчатое колесо привода смазочного насоса изготовлено из стали 15Х и имеет твердость HRC 54-58. При износе зубьев до толщины менее 2,1 мм и износе поверхности отверстия под штангу до диаметра более 7,4 мм зубчатое колесо заменяют. Износ поверхности зубчатого колеса под втулку до диаметра менее 13,92 мм можно восстановить хромированием с последующим шлифованием до нормального размера 14 — о.озз мм.
Корпус смазочного насоса изготовлен из алюминиевого сплава АЛ 10В с твердостью НВ 70. Если на корпусе имеются трещины, обломы любого размера и расположения и износ поверхности отверстия под зубчатое колесо до диаметра более 21,15 мм для мотоциклов К-750М, «Днепр-12» и «Урал» и более 29,575 мм для мотоциклов «Днепр», корпус заменяют.Корпус насоса при ремонте может иметь следующие дефекты:
износ поверхности отверстия до диаметра более 9,06 мм — обработать отверстие до ближайшего ремонтного размера 9,15+0016 и 9,30+0016 мм под ремонтные зубчатые колеса, а для двигателей мотоциклов «Днепр» — до размера 13,119 и 13,319 мм также под соответствующие ремонтные зубчатые колеса;задиры, забоины на торцовой поверхности — обработать поверхность и притереть. При контроле на краску прилегание должно быть не менее 70%;
срыв резьбы отверстия более трех ниток — рассверлить отверстие и нарезать резьбу ремонтного размера Мб под ремонтный болт.Корпус смазочного насоса мотоциклов «Днепр» К-650, МТ-9 и МТ-10-36, который изготовлен из алюминиевого сплава АЛ5 твердостью НВ 65, дефектуют и ремонтируют аналогично.
Ведущее зубчатое колесо смазочного насоса изготовлено из стали 45 и имеет твердость HRC 20-30. При наличии износа зубьев до толщины менее 2,0 мм, по окружности до диаметра менее 20,75 мм и по длине до величины менее 5,88 мм зубчатое колесо заменяют.При ремонте ведущее зубчатое колесо может иметь следующие дефекты:
износ поверхности под корпус до диаметра менее 8,96 мм — хромировать и шлифовать поверхность до нормального или ремонтногоразмера 9,151о,О27 и 9,31о;<>27 мм;
износ поверхности хвостовика под муфту до диаметра менее 6,8 мм — хромировать и шлифовать поверхность до нормального размера.Крышка корпуса смазочного насоса изготовлена из стали 45 и имеет твердость HRC 35-40. При наличии на крышке трещин обломов любого размера и расположения, а также при износе до толщины менее 2,5 мм крышку заменяют. При наличии на поверхности рисок, задиров ее обрабатывают до устранения дефектов, но до размера по толщине не менее 2,5 мм. При контроле краской прилегание должно быть на площади не менее 70%.
Сапун изготовлен из стали 35-45. При наличии трещин любого размера и расположения и при износе поверхности под крышку распределительной коробки до диаметра менее 41,8 мм сапун заменяют, При износе поверхности отверстия под штифт до диаметра более 5,9 мм просверливают новое отверстие нормального или ремонтного размера для ремонтного штифта под углом 180° к старому отверстию. Старое отверстие заваривают и зачищают заподлицо с основным металлом.Картер двигателя отлит из алюминиевого сплава АЛ5 и имеет твердость НВ 70,
Картер может иметь следующие дефекты:износ поверхности отверстия до диаметра более 150 мм — картер ремонту не подлежит;
пробоины размером до 20X20 мм — заделать наложением заплат с помощью эпоксидной композиции или сварки;трещины, не выходящие на посадочные поверхности и плоскости разъема, длиной менее 40 мм — заделать эпоксидной композицией или заварить;
износ поверхности отверстия под подшипник до диаметра более 52,03 мм — хромировать поверхность наружного кольца подшипника и затем обработать по месту до получения нормальной или допустимой посадки с зазором 0,043 мм;износ поверхности отверстия под корпус подшипника до диаметра более 77,05 мм — обработать отверстие до ближайшего ремонтного размера 77,0+0>03; 77,4+°.03; 77,6+°.°3; 77,8+°.03; 78,0+°.03 мм под ремонтный корпус подшипника;
износ поверхности отверстия под втулку до диаметра более 26,07 мм — обработать отверстие до ближайшего ремонтного размера 26.2+0033; 26,4+0-033; 26.6+0-033 мм под ремонтную втулку распределительного вала (кроме двигателей мотоциклов «Днепр» К-650, МТ-9 и МТ-10);износ поверхности отверстия под втулку до диаметра более 18,06 мм — обработать отверстие до ближайшего ремонтного размера 18,2+°.°45; 18,4+о.°45 и 18,б+о,о45 мм под ремонтную втулку;
износ поверхности отверстия под направляющую толкателя до диаметра более 24,1 мм — обработать отверстие до ближайшего ремонтного размера 24.2+0-045; 24,4+°045 и 24,6+0-045 мм под ремонтную направляющую толкателя;коробление плоскости разъема картера с цилиндром более 0,1 мм — обработать плоскость разъема до устранения недопустимого коробления;
ослабление посадки шпилек при срыве резьбы в резьбовых отверстиях более двух ниток—рассверлить дефектное резьбовое отверстие и нарезать резьбу ремонтного размера М8, М10 и М12 под ремонтную шпильку. После ремонта картер очистить от стружки, а поверхность зачистить от заусенцев и забоин.Крышка распределительной коробки двигателей тло-тоциклов К-750М и «Днепр-12» изготовлена из алюминиевого сплава АЛ 10В и имеет твердость НВ 65.
Крышка может иметь следующие дефекты:трещины, не выходящие на посадочные поверхности и плоскости разъема, а также трещины, идущие от отверстий под винты крепления к картеру до наружного контура детали — разделать трещины под заливку эпоксидной смолой или заварить и затем зачистить шов заподлицо с основным металлом;
коробление плоскости разъема крышки более 0,1 мм — устранить так же, как и коробление картера двигателя;износ поверхности отверстия под сапун — обработать по месту до получения нормальной или допустимой посадки с зазором 0,4 мм;
износ отверстия под штифт — отверстие обработать до ближай шего ремонтного размера
Передняя крышка картера изготовлена из сплава АЛЮ. Она может иметь обломы приливов, не выходящие на поверхность крышки. Облом можно устранить приставкой. Для этого обрубают неровные края облома, определяют форму и размер приставки, затем ножовочным станком отрезают приставку (от выбракованной алюминиевой детали) и подгоняют ее к месту для приварки. Зазор между приставкой и краями облома должен быть не более 2...3мм. Снимают с наружной стороны облома и приставки фаски под углом 45° на глубину 2..Л мм, устанавливают крышку на сварочный стол и закрепляют в положении, удобном для сварки, приваривают приставку и зачищают сварочный шов заподлицо с основным металлом.
Поддон двигателя может иметь следующие дефекты:трещины — устранить газовой сваркой, применяя горелку ГС-53 с наконечником № 2, а для присадки — проволоку СВ-08 диаметром 3...4 мм. После сварки зачистить шов заподлицо с основным металлом. На пробоины можно наложить заплаты на эпоксидной композиции или приварить их (по всему периметру);
коробление плоскости разъема поддона с картером более 0,2 мм — выправить поддон до устранения коробления с помощью молотка на разметочной плите;вмятины в поддоне глубиной более 0,6 мм — выправить поддон до устранения недопустимых вмятин;
помятость сливной трубки или срыв резьбы более двух ниток — заменить трубку.Маховик с пальцами сцепления при ремонте может иметь дефекты:
износ конусной поверхности под цапфу коленчатого вала более допустимого (допускается утопание калибра от номинального положения не более 0,4 мм) — хромировать или обварить поверхность и обработать до нормального размера;износ боковых поверхностей шпоночного паза до ширины более 6,04 мм — подогнать шпонку по месту с обеспечением допустимой посадки с зазором 0,055 мм или заварить и фрезеровать шпоночный паз до нормального размера;
ослабление посадки пальца сцепления при увеличении диаметра отверстия маховика более 12,035 мм — обработать дефектное отверстие до ближайшего ремонтного размера 12,1+°.°35; 12.2+0035 мм под ремонтный палец;износ поверхности пальца под диски сцепления до диаметра менее 11,8 мм — заменить палец. Пальцы в маховик запрессовать с натягом 0,01...0,08 мм. Торцы пальцев должны лежать в одной плоскости. В случае перепрессовки некоторых пальцев торцы должны
быть вновь прошлифованы; биение их друг относительно друга допускается не более 0,1 мм на радиусе 102 мм;срыв резьбы пальца более трех ниток — заменить палец. После ремонта маховик проверить на статическую балансировку. Допускается неуравновешенность 15:10~4 Н-м. При необходимости удалить металл сверлением отверстий диаметром 9 мм и глубиной не более 10 мм на радиусе 100 мм.