Способ ремонтных размеров. Одну из изношенных деталей сопряжения, обычно более дорогую или сложную, механически обрабатывают до установленного размера, а другую деталь заменяют восстановленной или новой, изготовленной также под ремонтный размер.
Способ дополнительных ремонтных деталей. Применяют при использовании заранее изготовленных деталей, которые устанавливают на специально подготовленные поверхности отверстий или валов и таким образом заменяют изношенную часть детали (вкладыши шатунов, поршни, поршневые кольца и др.).Устранение дефектов давлением. Основано на использовании пластических свойств материала деталей. Применяют для восстановления размеров изношенных поверхностей под подшипники (накатка поверхности), усталостной прочности и жесткости (обработка пружин профилированным роликом) и деформированных деталей (втулок и др.).
Устранение дефектов гальваническим и химическим наращиванием металла (хромирование, осталивание, меднение, цинкование). Отсутствие нагрева детали и структурных изменений в металле, что выгодно отличает этот способ от других (сварки, наплавки и др.).Электроискровой и плазменный способы. Для легирования и наращивания изношенных поверхностей деталей, более дорогих и трудоемких в изготовлении.
Пайка. Ликвидируют трещины и используют при ослаблении прочности спая в агрегатах электрооборудования.Сварка и наплавка — наиболее распространенный способ восстановления деталей. Это объясняется возможностями восстанавливать детали, изготовленные из различных металлов и имеющих самые разнообразные дефекты. )
Дефекты деталей из алюминиевых сплавов (трещины, пробоины, обломы, изношенные поверхности отверстий) можно устранять электродуговой сваркой с применением электродов марки ОЗА-2. Электроды хранят в сухом вентилируемом помещении; не использованные в пределах одного месяца со дня их изготовления электроды перед употреблением необходимо прокаливать при температуре 22О...23О°С в течение 1 ч. Для заварки трещины вырубают неглубокую канавку по всей длине трещины. Шлаки, покрывающие шов, после сварки смывают водой и одновременно очищают металлической щеткой. Перед сваркой деталь необходимо предварительно подогреть до 15О...25О°С.При восстановлении деталей мотоциклов из алюминиевых сплавов используют электроды диаметром 3...5 мм. Сила тока должна
быть 125...160 А, длина дуги равна диаметру электрода, скорость сварки — 0,4...0,6 м/мин.Восстановление деталей эпоксидными композициями и клеем.
Используемые для ремонта деталей способы, в частности электро-и газовая сварка, наплавка, хромирование, металлизация, требуют специального оборудования и производственной базы и поэтому часто неприемлемы для водителя. Эпоксидные смолы и на их основе различные композиции и клеи можно использовать для ремонта в полевых условиях и в ряде случаев без демонтажа агрегатов и узлов. Рассмотрим эти методы более подробно.Эпоксидными композициями можно восстанавливать следующие детали: картер двигателя и его крышки, головку цилиндра и ее крышку, поддон картера, картер коробки передач и его крышки, корпус карбюратора, топливный бак, грязевые щитки и кузов тележки (пробоины и трещины). Можно также ремонтировать изношенные поверхности в сопряжениях вал — подшипник, подшипник — гнездо подшипника и закреплять ослабевшие шпильки и штифты.
Ремонтируемая деталь должна быть предварительно очищена от ржавчины и грязи механическим или химическим способом. Механическую очистку производят шабером, напильником, наждачной бумагой, шлифовальным кругом или обработкой на металлорежущих станках. Химически очищают (обезжиривают) ацетоном, бензином Б-70 или растворителями № 646 или № 648 и РДВ. При обезжиривании следует применять только волосяные кисти или щетки.Во всех случаях для улучшения механического сцепления эпоксидной композиции с ремонтируемыми поверхностями последние обрабатывают с повышенной шероховатостью.
Иногда на поверхности ремонтируемой детали наносят зубилом неглубокие насечки по трещине или вокруг пробоины. Отверстия или кан-авки закрывают паклей или асбестовым шнуром. После такой подготовки обезжиривают, затем выдерживают деталь при температуре 18...23°С в течение 5 мин до полного высыхания растворителя. Подготовленность поверхности определяют с помощью капли воды: если вода расплывается и смачивает поверхность, то сцепление ее с эпоксидным составом будет хорошим.При заделке на детали трещины поверхность вокруг нее зачищают на 10...15 мм и притупляют кромки, на очищенные и обезжиренные края трещины наносят шпателем эпоксидную композицию, затем накладывают заплату из стеклоткани (или другого плотного хлопчатобумажного полотна) толщиной 0,3...0,4 мм и прикатывают роликом, как указано на рисунке 1. На заплату и поверхность детали наносят второй слой композиции и накладывают вторую заплату и т. д. Всего на пробоину накладывают 3—8 слоев ткани, последний слой покрывают композицией. После полного отвердения неровности обрабатывают наждачным кругом.
В случае установки на пробоину металлической накладки толщиной 0,5...0,8 мм по контуру пробоины просверливают отверстия диаметром 1,5...2,0 мм (рис. 2) и зачищают накладку и поверхность детали вокруг пробоины. Затем обезжиривают кромку пробоины, зачищенный участок поверхности пробоины и металлическую наклад-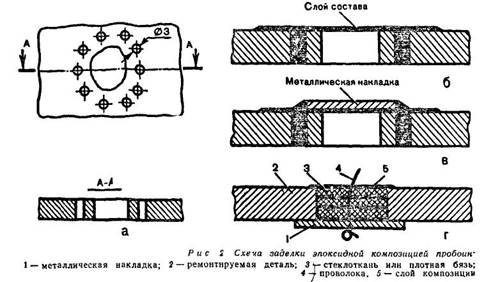
Иногда на металлическую накладку кладут еще несколько накладок из стеклоткани, с прикаткой роликом (рис. 2,г).
Для заделки пробоин и трещин на картерах и других деталях целесообразно применять эпоксидный компаунд К-П5(СТУ 30—14148—63) с наполнителями. Состав композиции (в весовых частях): компаунд К-П5-12, наполнитель (один из следующих номеров): 1) стальной порошок—10 и графит — 2; 2) графит — 7; 3) слюда молотая — 6; 4) алюминиевая пудра — 4,5. Отвердитель — АФ-2 (ТУ 264—70).
Композицию приготовляют непосредственно перед употреблением, так как при введении в нее отвердителя может произойти ее разогрев и быстрое отвердение. Композицию желательно готовить в плоских металлических, картонных или пластмассовых противнях в количестве, необходимом для разового применения (150...200 г), так как срок годности ее не более 35...40 мин. При изготовлении композиции из эпоксидной смолы последнюю подогревают в водяной ванне до температуры 5О...6О°С и заливают в противень, так чтобы толщина слоя была не более 10...15 мм. После этого в нее при тщательном перемешивании в течение 5 мин вводят пластификатор — дибу-тилфтолат. К полученной смеси добавляют наполнитель, перемешивают еще 5 мин и охлаждают до температуры 18...23°С, а затем частями вводят отвердитель в смесь и тщательно перемешивают в течение 4...5 мин.Наносить композицию на ремонтируемую деталь и накладку следует только деревянным, металлическим или резиновым шпателем. Затвердевает композиция в зависимости от температуры среды. При температуре 18...23°С выдержка дается в течение 24...36 ч, при 60°С — 2...3 ч и при 100°С —0.5...1 ч.
Для ремонта изношенных поверхностей деталей, работающих в сопряжениях вал — подшипник, подшипник — гнездо подшипника, и для закрепления ослабевших шпилек и штифтов рекомендуются эпоксидные пасты, не стекающие с вертикальной стенки при температуре 18...23°С. Для приготовления пасты в эпоксидную смолу вводят один из наполнителей в количестве, указанное в таблице 2.Таблица 2. | Составы эпоксидных паст, % от массы смолы | |
Наполнитель | Смола ЭД-16 | Смола ЭД-20 |
Железный порошок Графит Алюминиевая пудра Бронзовая пудра Кварцевая мука Портландцемент | 200 80 25 130 230 200 | 160 40 20 80 150 120 |
Восстановление клеем сопряжения подшипник — гнездо возможно только в случае, когда зазор между ними не превышает 0,1...0,2 мм. При восстановлении гнезд под подшипники клей наносят тонким слоем на предварительно обезжиренную поверхность гнезда и подшипника, затем устанавливают подшипник в гнездо и выдерживают 24 ч при температуре 18...23°С или 3 ч при температуре 60 °С.
Для этих иелей рекомендуются клеи: ВС-ЮТ, ВС-350 и ВК-32-200. Область применения клеев при ремонте представлена на рисунке 3.